Tour: Materials and Processes
Moving beyond retailing and wholesaling often involves costing and production.
Materials
Controlling food costs is critical for restaurants. If cost of materials moves higher than 27% to 29% of menu prices, the restaurant is unlikely to survive. Here is a good article from Forbes.
Just as accounting uses a Chart of Accounts, costing uses a Chart of Materials.
This restaurant manager has listed costs and calories per kilogram of ingredients used in his menus.
(Sumer does not have built-in measurement systems, so use of metric or British units is up to the manager.)
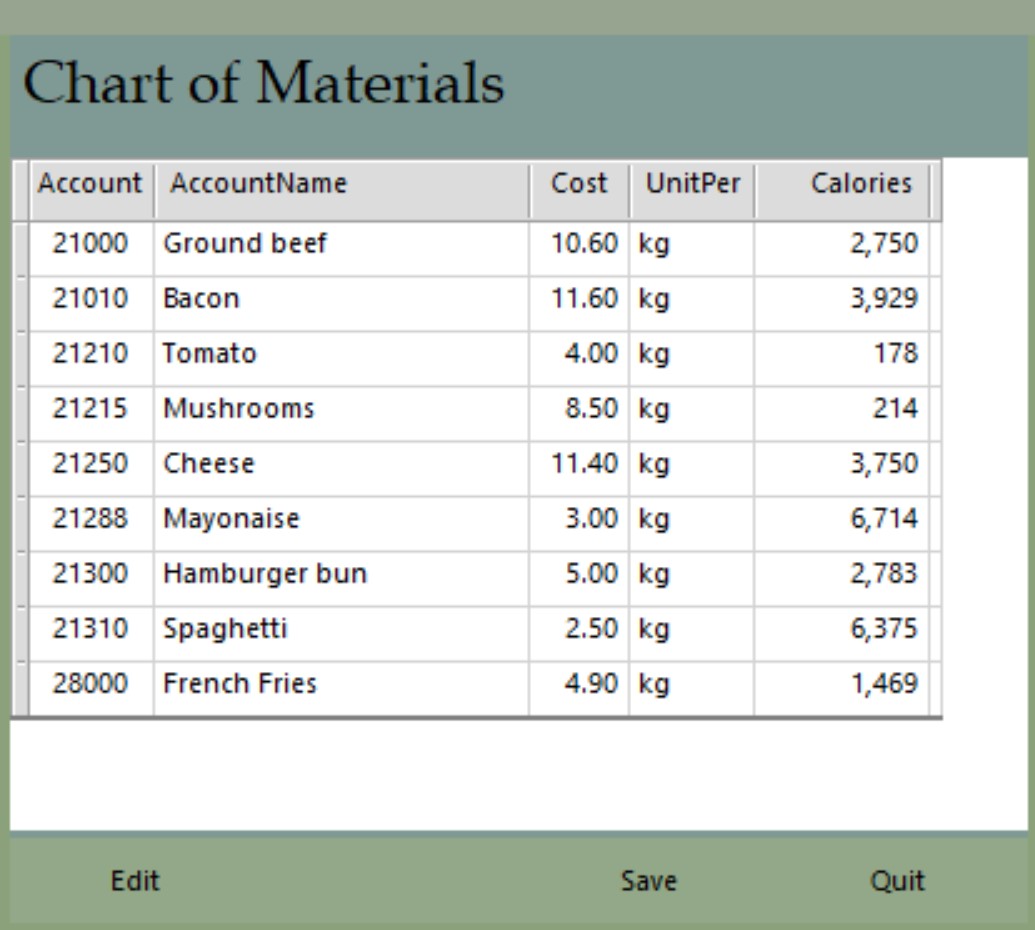
Simple cost of materials calculations can be done manually on spreadsheets or on paper. The Sumerians probably did them on clay tablets—maybe even for hamburgers; they had beef and bread. Also beer.
This menu item should sell at a dine-in restaurant for about $10.00.
Sumer's' Bill of Materials and Processes (BOMP) form is set up using the same spreadsheet format as the other forms in Sumer involving popups, expressions, footer rows, and so on.
The advantage of a relational solution as with Sumer is that changing a material cost in the Chart of Materials automatically updates the prices in the Bill of Materials and Processes.
It is even possible to link or relate the cost in Chart of Materials to price in Inventory so that Chart of Materials always reflects the most recent purchase price of each ingredient.
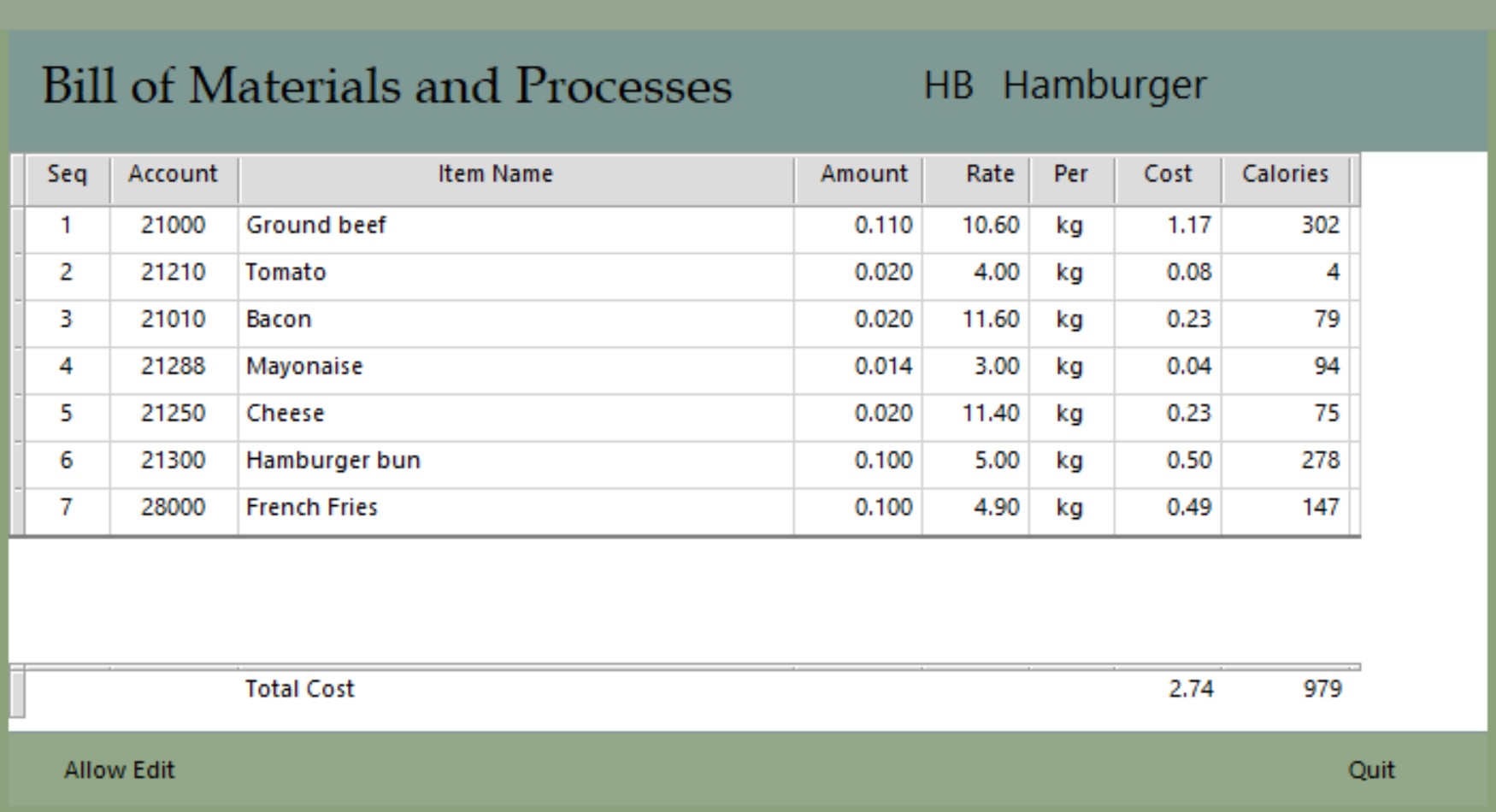
Taking the relational advantage a bit further, Sumer can summarize all Costs of Goods Sold by automatically extracting the cost of each menu item from the Bill of Materials and Processes and including it with the Sales report for an accurate costing of sales per item.
Small businesses often use a simpler method to estimate Cost of Goods Sold: at the end of the week they take a physical inventory and subtract their current inventory value from their beginning inventory value. Of course this involves manually calculating the current inventory value, either on paper with a spreadsheet. And any new stock purchased during the week must also be subtracted back out.
Also this method does not catch possible shrinkage from either employee or customer pilfering. Nor does it provide a breakdown of revenue vs cost for each individual item.
Also it's a lot of work, so too often managers are tempted to skip it.
Big restaurant chains certainly rely on relational costing, but the owner of an individual restaurant may not feel justified in paying for an extra Costing + Inventory module.
Sumer does not use modules. The pricing model described in Tour does not charge for reports. So this relational costing technique is available to any client essentially for free by simply downloading and customizing the template.
Processes
Manufacturing can include a complex series of steps involving labor, equipment, transport, conversion of materials, sub-assemblies, inspections, quality control, piecework, inventory management, and more.
Sumer originated as an integrated management system for a garment manufacturer and retailer in Bali, Indonesia—Uluwatu Handmade Balinese Lace. Over 500 workers cut, sewed, applied lace, washed, ironed, and packed the garments. Each style involved a unique sequence of production processes, and every garment needed to be traceable to each worker who contributed to it.
It was a fairly extreme case of production managment, but Sumer was designed to handle complex manufacturing.
The Chart of Materials and Processes breaks down each process into standards based on time or completed operation.
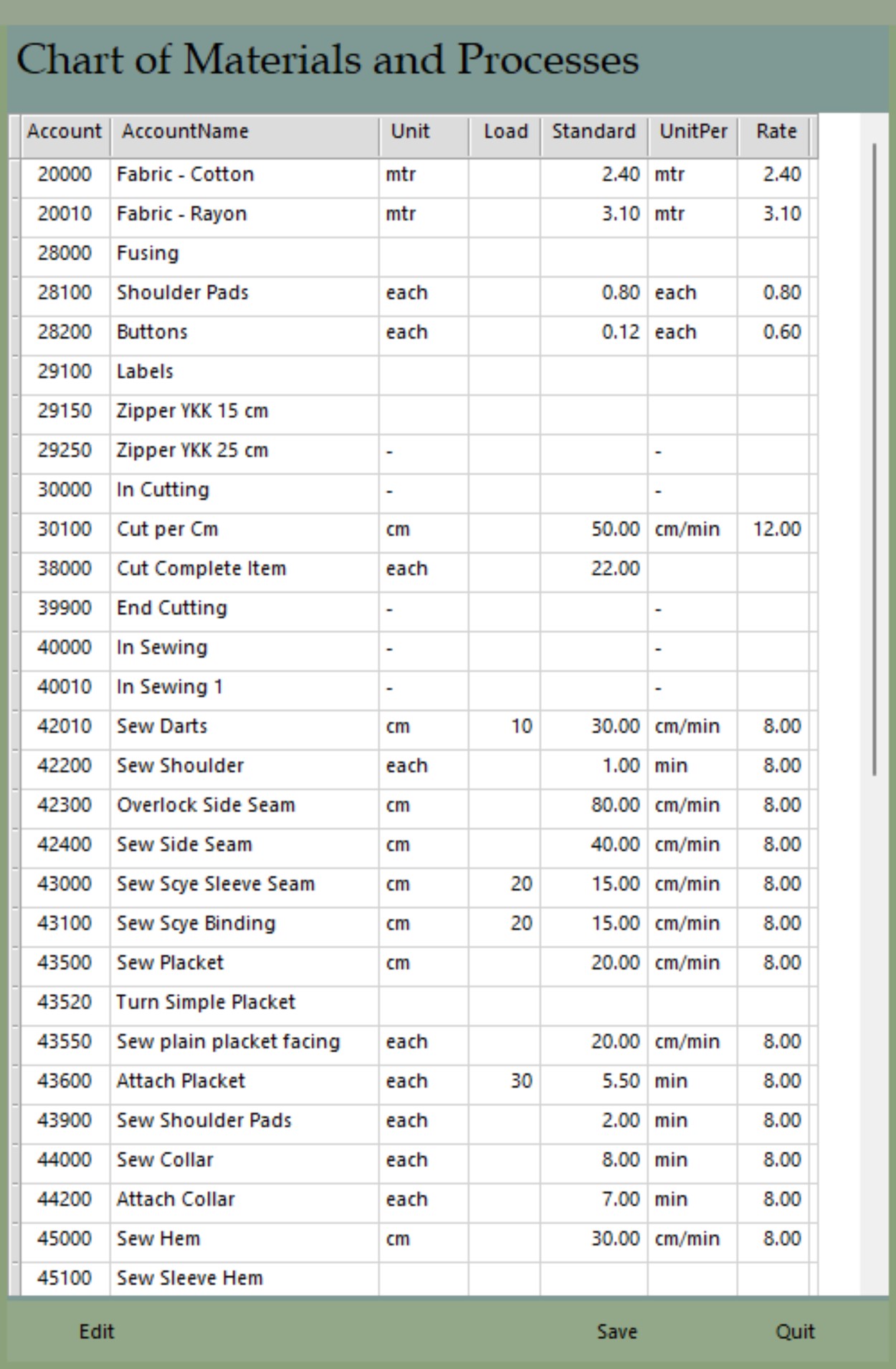
The following example lists both Material and Processes for a garment called the Darla Dress.
The top three rows are a Bill of Materials, showing a total material cost of 5.92.
The remaining rows are a Bill of Processes listing events in the order with which they proceed through the factory, from Cutting, Sewing, Lace, and Finishing.
The manager of each department would have a tablet computer with a graphic overlay Event form so they can quickly enter each individual item as it is finished and passed to the next department.
The BOMP enables:
- Accurate product costing,
- Control of production paths,
- Calculation of time and piecework wages,
- Inventory tracking of Work in Process.
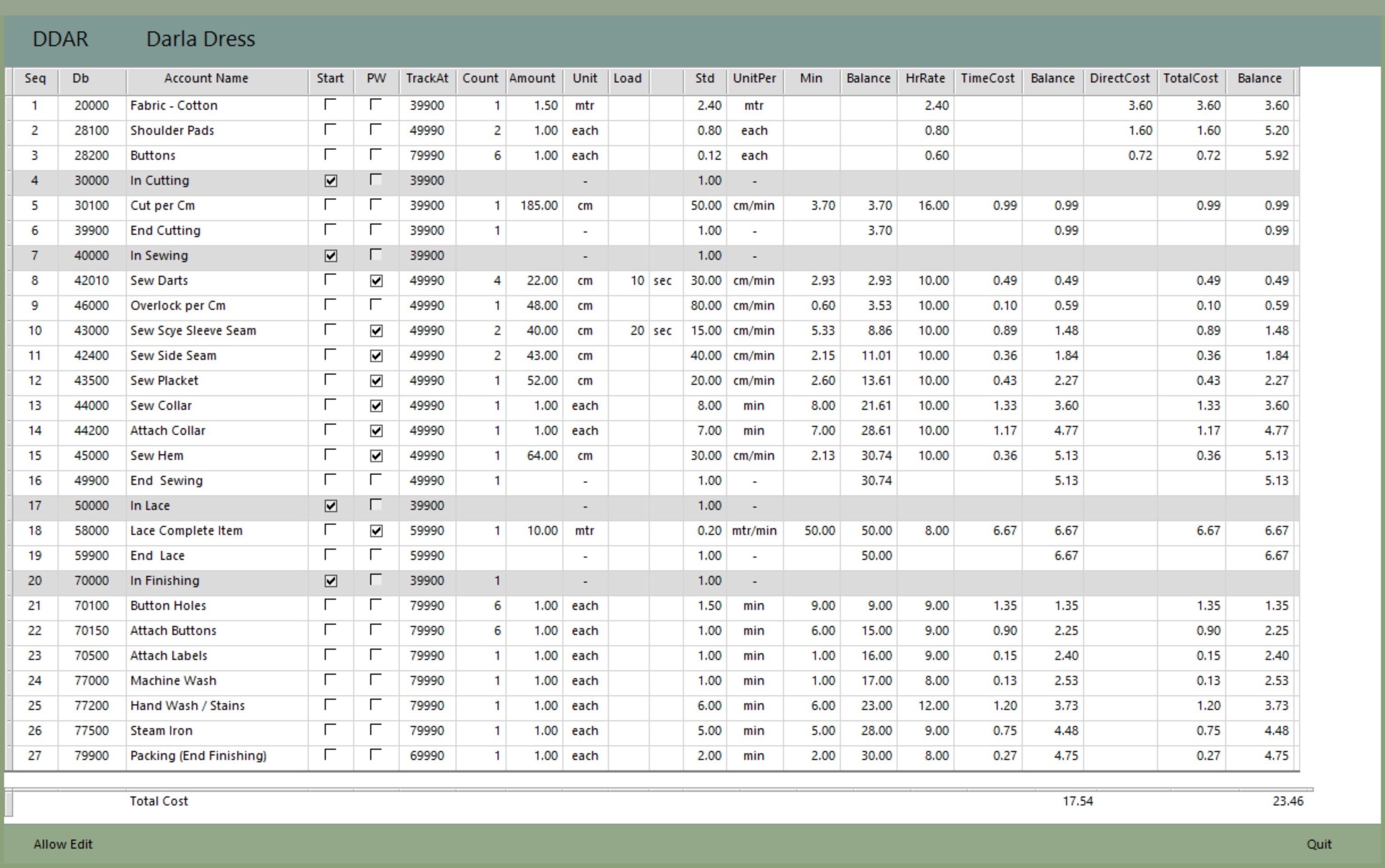
The 'Start' column breaks production into four departments and allows Sumer to search for and sum subtotals.
'PW'stands for 'piecework'; workers are credited with piecework incentive pay for these operations.
'TrackAt' tells Sumer at what point in time to credit piecework and/or inventory for a material or operation. Crediting inventory at certain points in the production process is often called 'flush-back.'
The remaining columns carry out the costing.
Built into Sumer is the ability to track work-in-process as individual items move through departments. Management has a real-time snapshot of what is currently in each department or in what departments items of a particular production run are located.
Sumer can also look up and apply piecework incentive pay for each worker based on the Bill of Materials and Processes for each garment the worker has produced.
But it is important to note...
This is the Chart of Materials and Processes without the rows and columns added in the templates.
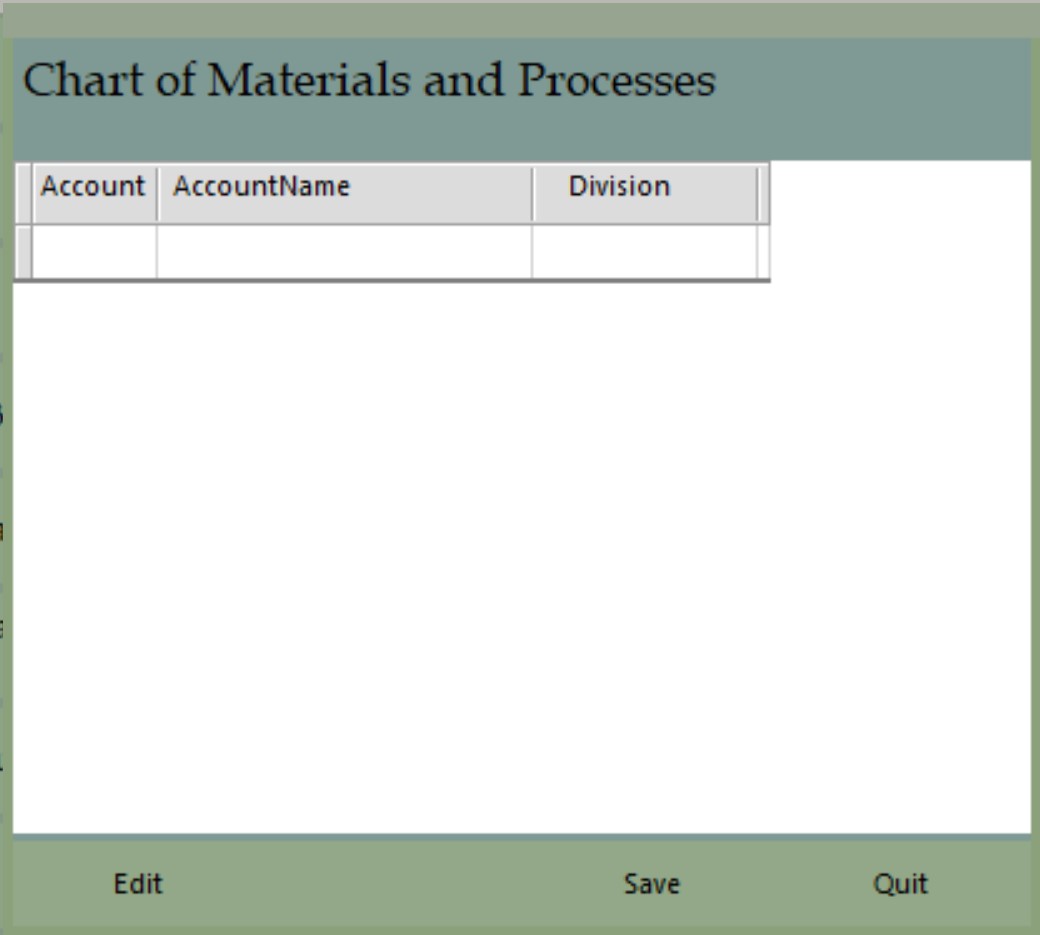
And this is the Bill of Materials and Processes (BOMP).
Everything else is added through the Setup Parameters form.
Like everything else in Sumer, the basic form is blank. As with Excel, the empty form has built-in capabilites that enable a user to shape it to their own needs.
The Bill of Materials and Processes has capabilites to interact with Entry, Report, and Inventory forms to build a production control suite for complex manufacturing processes.
No coding required. A good knowledge of business management is enough.
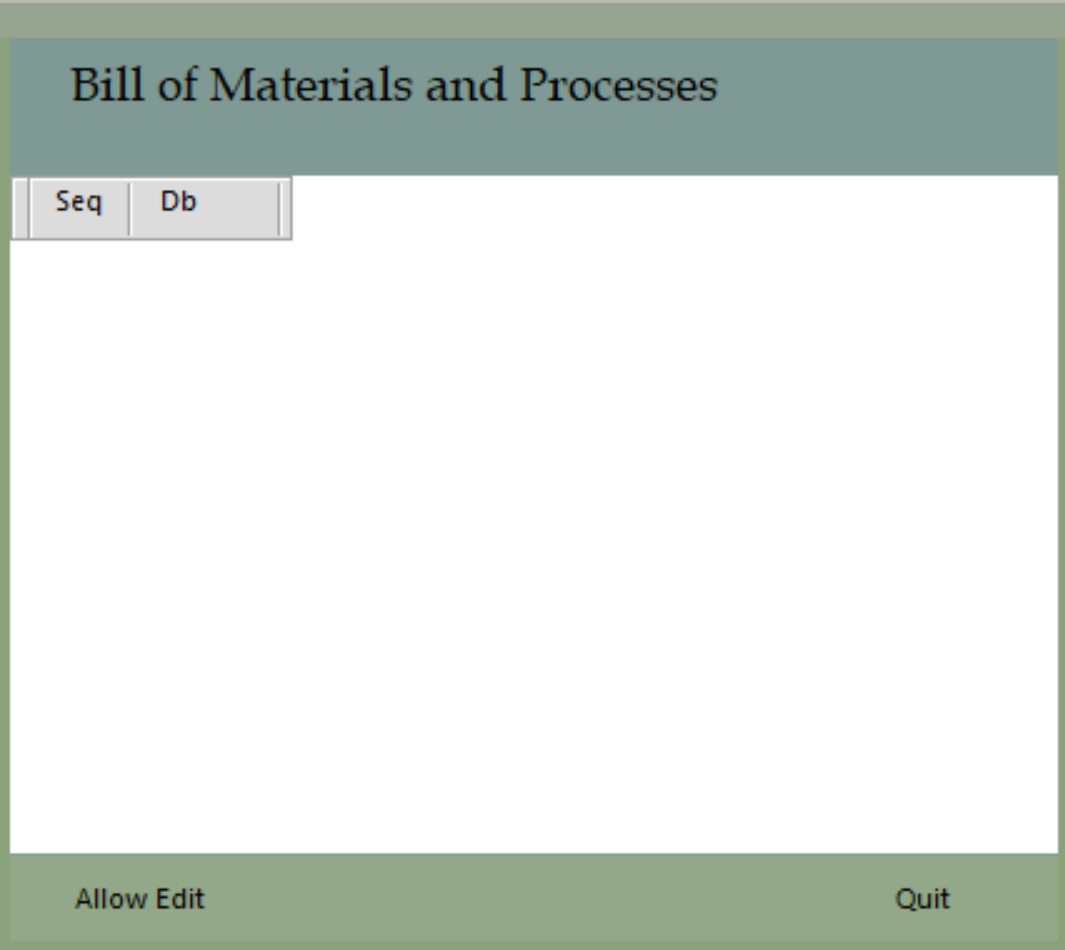